事例紹介
建材・住宅設備機器メーカー様事例
兵庫県に製造工場と物流センターを持つA社様では、製造部門の統合により商品の出荷量が増加し、配送に必要な車両台数がこれまでの30%増となりました。
しかし物流会社が多く存在する大阪府周辺から工場が遠いことから車両の確保が困難であり、また車両が用意できてもコストが掛かるため、工場から直接納品先様へ配送するのではなく、近畿圏内に拠点を設置し、クロスドッキング方式であるスルー便へ配送スタイルを変更したいと考えていました。
改善前の課題
- 出荷工場が大阪より70~80km離れているため、出荷量の波動による増車手配が困難
- 積載量にかかわらず、車建運賃にて工場から納品先までの配送を算出するためコスト増
- 大阪府周辺の物流会社が多く、集車する際に空車回車が発生しコスト増
- 工場内に多数の車両が不規則に入構するため、待機時間の発生及び施設内安全上の管理負担リスクが大きい
- 積込み車両の時間波動により積込みバースの確保およびピッキング調整作業が発生
- 入構車両時間が集中し順次対応していくため、ピッキング、積込み作業員の労働時間が超過
- ひとりで荷降ろしが不可能な商品をツーマン配送にする際、助手の手配を現地調達するのが困難
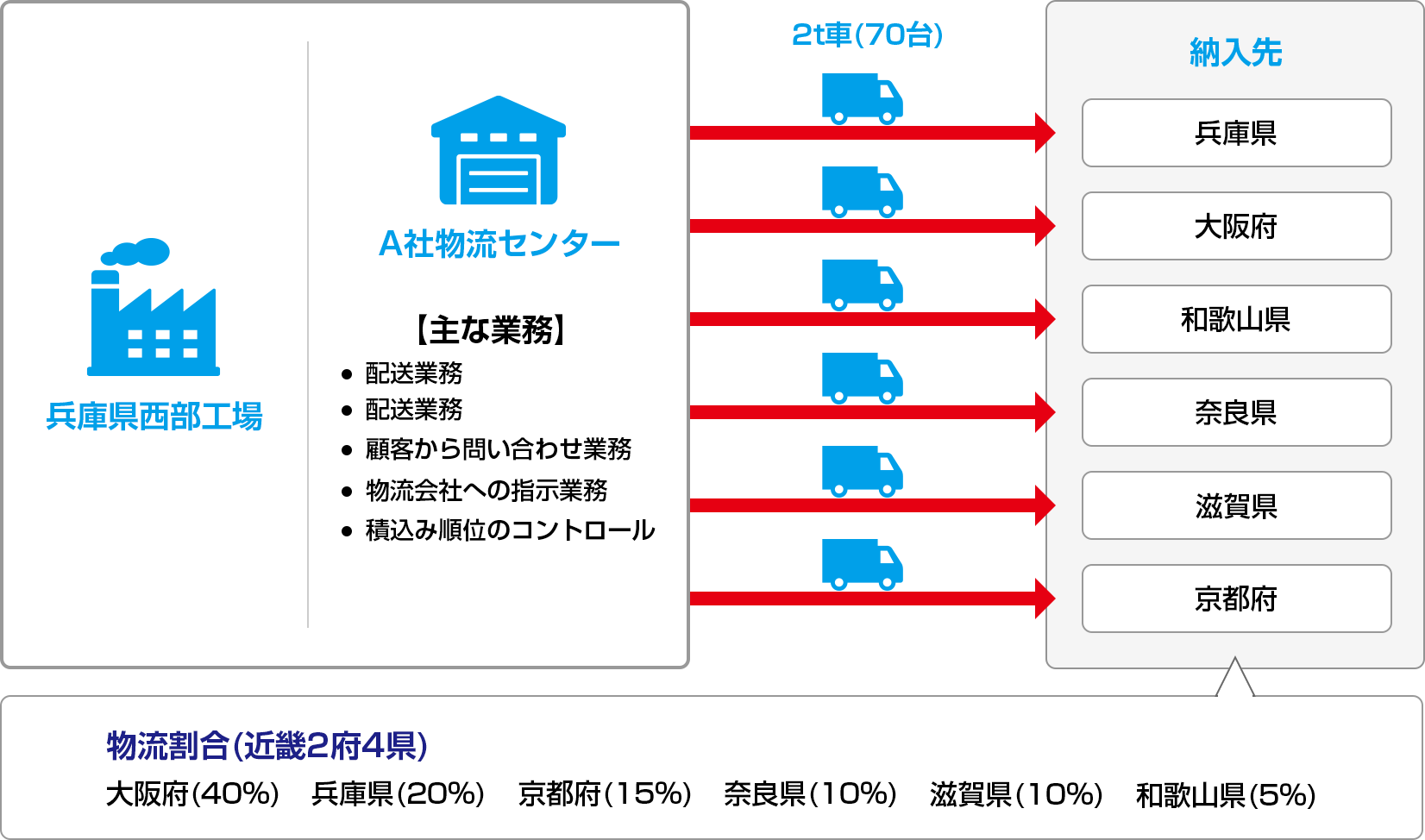
改善施策
- 大阪・京都への配送については、つばめ急便のセンターを再配拠点として活用
- 工場から納品先への直送形式から、工場から再配拠点を通過し納品先へと配送ルートを変更
- 配送形式を貸切(チャーター便)から共同配送便(2トン、4トン車両積み合せ)に変更しコスト削減
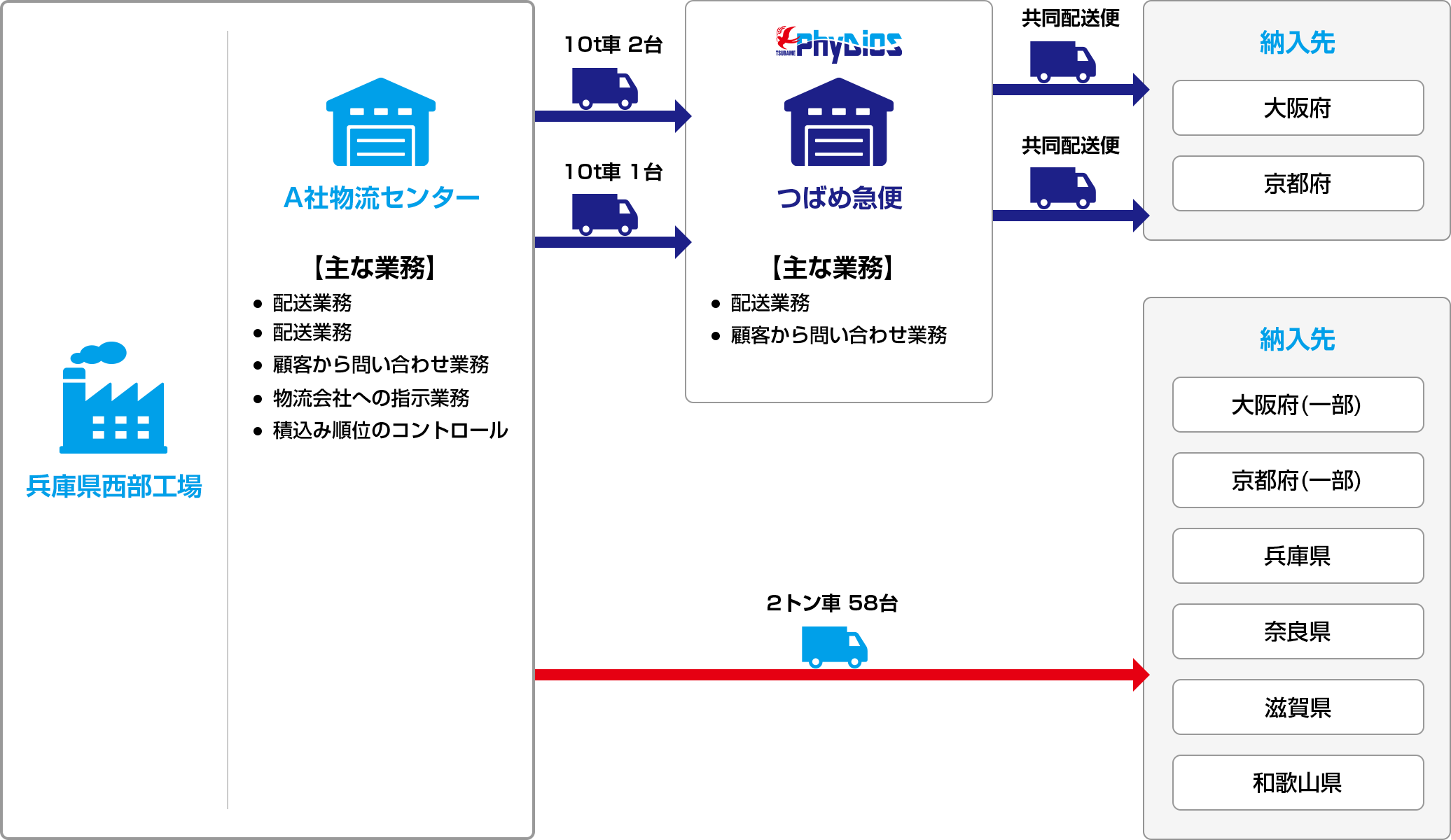
改善施策
- 10トン3台(2トン12台分)を固定できた事で波動対応が可能、集車業務が安定
- 配送料が拠点から納品先までの重量建て運賃(変動運賃)になったためコスト減
- 工場内に入構する車両が減少し、安全管理面での負担が軽減
- 幹線車両を定刻時間に工場へ入構させることで、出荷体制が安定
- 幹線車両を定刻時間に工場へ入構させることで、積込み時間の効率化が図れ作業員の労働時間の低減が実現可能
- スルー便にすることでツーマン配送の助手手配が容易(荷降ろしするタイミングを見計らい、当日手配も可能)
- 工場への入構台数を減らすことで環境負荷の低減(CO2削減27%)